F-35 : Origins Part I- The Checkered History of Joint Service Aircraft
<< Pavia,Italy, AUG-7-2024 >> << Dallas,Texas, MAY-7_2025 clean up DOD acquisition system section >> F-35 : Origins Part I- The Checkered History of Joint Service Aircraft This article explores the origins of the F-35 program, tracing its development to the challenges and lessons learned from earlier attempts at creating multi-service aircraft platforms, as well as the shifting geopolitical and fiscal realities at the end of the Cold War. We will examine the successes and failures of previous joint-service aircraft initiatives, shedding light on how these experiences informed subsequent efforts. Additionally, we will consider the strategic recalibration faced by the United States as the Soviet threat waned, introducing new funding constraints and priorities for defense planning. Finally, the article will delve into the processes by which the Department of Defense designs and builds military aircraft, analyzing how the F-35 program aligns with and deviates from these established practices. With that context established, let us begin by reviewing earlier attempts at joint-service aircraft to understand the foundation on which the F-35 program was built. The F-4 Phantom II - An Off the Shelf Tri-Service Attempt The McDonnell Douglas F-4 Phantom II emerged as one of the most successful multi-role combat aircraft of the Cold War, serving simultaneously with the United States Navy (USN), United States Air Force (USAF), and United States Marine Corps (USMC). Originally designed as a carrier-based interceptor for the USN in the late 1950s, the F-4 proved so versatile that it was adopted by the USAF and USMC for a wide range of roles, including air superiority, ground attack, and reconnaissance. This decision was driven by the aircraft’s exceptional performance, featuring twin engines, advanced radar, and the ability to carry a heavy payload of both missiles and bombs. Its adaptability and raw power made it an appealing choice across multiple branches of the U.S. military. One of the key advantages of using the F-4 as a joint-service aircraft was the economies of scale achieved in production and maintenance. Sharing a common platform reduced costs associated with manufacturing, logistics, and training, as all three branches could standardize their supply chains and pilot training programs. The F-4’s multi-mission capability also provided operational flexibility; its speed, payload, and advanced avionics allowed it to excel in both air-to-air and air-to-ground roles, making it a formidable force across theaters. The Phantom’s adaptability was further demonstrated in Vietnam, where it was deployed in diverse roles, including close air support, tactical bombing, and air defense. However, the decision to use the F-4 as a joint-service aircraft also came with significant drawbacks. The Phantom was initially designed without an internal cannon, relying entirely on missiles for air combat—a decision influenced by the Navy’s doctrine that emphasized beyond-visual-range engagements. This limitation proved problematic in close-range dogfights during Vietnam, where USAF and USMC pilots often found themselves at a disadvantage against more maneuverable adversaries. Additionally, the F-4’s large size and weight, optimized for carrier operations, made it less agile compared to dedicated land-based fighters like the MiG-21, which challenged its effectiveness in air-to-air combat. Another disadvantage was that the F-4 could not be perfectly tailored to the specific needs of each service. While it was effective as a jack-of-all-trades, its compromises made it less optimal in specialized roles. For instance, the Navy had to contend with the Phantom’s high landing speeds during carrier operations, while the USAF’s use of the aircraft in ground attack missions was hindered by its vulnerability to anti-aircraft fire due to its size. Despite these issues, the F-4 Phantom II remains an iconic example of a joint-service aircraft, praised for its longevity, versatility, and significant impact on Cold War-era combat aviation. The USAF itemized all the issues with the F-4 and eventually developed the F-15 Eagle which to this day remains a potent Air Superiority Fighter. The only real issue with the F-15 is its lack of stealth. The F111 - A Custom Built Duo-Service Attempt The General Dynamics F-111 Aardvark was developed as a pioneering multi-role combat aircraft, originally intended to fulfill a joint service requirement for both the United States Air Force (USAF) and the United States Navy (USN). Initiated in the early 1960s under Secretary of Defense Robert McNamara's advocacy for cost-efficient joint-service programs, the Tactical Fighter Experimental (TFX) program aimed to produce a single aircraft design adaptable for various military missions. The USAF sought a high-speed, low-altitude interdictor capable of carrying heavy payloads deep into enemy territory, while the USN needed a carrier-capable fleet defense interceptor to counter long-range Soviet bombers and missiles. The resulting design featured advanced technologies such as variable-sweep wings, afterburning turbofan engines, and a terrain-following radar. Despite its innovative features, the F-111 faced significant design challenges due to conflicting service requirements. The USAF's specifications called for a heavy aircraft optimized for long-range strike missions, while the USN demanded a lighter, more agile platform for carrier operations. Meeting these divergent needs led to compromises, such as the F-111's weight and size, which posed difficulties for carrier-based operations. Additionally, the complex variable-sweep wing mechanism and the aircraft's sophisticated avionics added to development delays and cost overruns. Although the F-111A variant eventually achieved success in USAF service, the USN's requirements proved too stringent for the airframe's inherent design. The USN's dissatisfaction with the F-111's suitability for its operational needs culminated in its withdrawal from the program in 1968. The Navy cited several issues, including the aircraft's excessive weight, which compromised its ability to operate safely from aircraft carriers, and its relatively poor maneuverability, which hindered its effectiveness as a dog fighter. Moreover, the F-111B, the Navy-specific version, suffered from performance shortfalls in speed, range, and payload capacity, further alienating naval leadership. By this time, it had become clear that the joint-service approach, while cost-effective in theory, was impractical given the fundamentally different mission profiles of the two branches. After abandoning the F-111B, the Navy turned to Grumman to develop the F-14 Tomcat, a dedicated fleet defense interceptor and air superiority fighter that more closely met its requirements. The F-14 retained some of the F-111's advanced technologies, such as the variable-sweep wing, while incorporating a lighter, more maneuverable design tailored to carrier operations. Meanwhile, the F-111 went on to serve successfully with the USAF in a variety of roles, including tactical bombing and electronic warfare, becoming a cornerstone of U.S. airpower until its retirement in the 1990s. The F-111 program highlighted the challenges of joint-service procurement and the importance of designing aircraft tailored to specific operational needs. Before leaving the subject of the F-111/F-14, its important to point out some of the problems were with the common propulsion system. The Pratt & Whitney TF30 afterburning turbofan engine, widely used in early versions of the F-111 and the F-14 Tomcat, faced significant operational challenges that impacted the performance and reliability of these aircraft. Originally designed for the F-111, the TF30 was the first afterburning turbofan engine, but its groundbreaking nature brought with it numerous technical issues. One of its primary problems was compressor stall, particularly during high-angle-of-attack maneuvers. These stalls often resulted from disrupted airflow into the engine, leading to sudden and dangerous losses of power. This issue was especially problematic in the F-14, where the engine's limitations significantly affected the aircraft's dog fighting capabilities and posed risks during carrier takeoffs and landings. Another major problem with the TF30 was its poor thrust-to-weight ratio and limited durability under combat conditions. The engine struggled to provide sufficient thrust, especially at low speeds or in high-performance scenarios, which made the aircraft reliant on it less competitive against adversaries like the Soviet MiG-23. Furthermore, the TF30's afterburner had a tendency to "blow out" during sudden throttle changes, a critical issue in combat situations where rapid power adjustments were essential. These shortcomings, combined with frequent maintenance needs and high failure rates, eventually led to the replacement of the TF30 in later F-14 variants with the more reliable and powerful General Electric F110 engines, highlighting the TF30’s inherent limitations as an early-generation turbofan. Curiously, the non after burning TF30 was used in the A-7 Corsair II and was quite reliable. But anyway, we digress ... JAST - A Multi Variant Custom Built Tri-Service Attempt ( Third Times a Charm ?) The USAF MRA program, short for the Multi-Role Aircraft program, emerged in the 1990s as an initiative by the United States Air Force (USAF) to develop a versatile, cost-effective fighter aircraft capable of excelling in both air-to-air combat and air-to-ground attack roles. This program reflected the post-Cold War emphasis on adaptability and efficiency in military aviation. With shifting strategic priorities and budget constraints following the dissolution of the Soviet Union, the USAF sought an aircraft that could replace aging fleets of specialized aircraft like the F-16 Fighting Falcon and the A-10 Thunderbolt II, consolidating capabilities into a single platform. The MRA program aimed to reduce logistical and operational costs while maintaining a technological edge in diverse combat scenarios. Although it did not ultimately lead to a standalone aircraft, the concepts and requirements explored under the MRA program influenced the development of subsequent USAF initiatives. Its emphasis on multi-role capabilities and affordability became key considerations in the later Joint Strike Fighter (JSF) program, which culminated in the F-35 Lightning II. The MRA program marked a transitional phase in military aviation, reflecting the USAF's efforts to align its resources and capabilities with the emerging security landscape of the 21st century. The USN AX/AFX program, launched in the 1990s, was a United States Navy initiative aimed at developing a next-generation attack aircraft to replace aging platforms such as the A-6 Intruder and the F-14 Tomcat in carrier-based operations. The program, initially called AX and later rebranded as AFX (Advanced Attack/Fighter Experimental), sought to deliver a stealthy, multi-role aircraft capable of penetrating advanced air defenses, conducting precision strikes, and maintaining air superiority. This effort was driven by the Navy's recognition of the need for a highly survivable and versatile platform in an era of emerging threats and rapidly advancing technology. The AFX design requirements emphasized stealth, range, payload capacity, and the integration of advanced avionics and sensors to ensure dominance in complex combat scenarios. Despite initial promise, the AFX program faced significant challenges, including escalating costs, evolving operational requirements, and inter-service competition with the Air Force's own programs, such as the F-22 and F-35. In 1993, the AFX program was ultimately canceled, with many of its goals subsumed into the broader Joint Strike Fighter (JSF) initiative, which sought to develop a multi-service aircraft. The JSF program later produced the F-35, which included a carrier-based variant tailored to the Navy's needs. While the AFX itself never materialized, its conceptual foundation influenced the development of modern naval aviation, demonstrating the Navy's commitment to advancing carrier-based capabilities in a changing strategic environment. Many of these defense programs were conceived during the Cold War. With the collapse of the Soviet Union in the early 1990s, the Pentagon recognized the need for a comprehensive reevaluation of defense priorities. In February 1993, it initiated a formal Bottom-Up Review (BUR) to develop strategies and policies for a post-Cold War world. At the highest level, the BUR identified a requirement for the U.S. military to be capable of simultaneously engaging in two major regional conflicts (MRCs). This envisioned scenarios such as a conflict akin to the Iraq War and a potential invasion of Taiwan occurring concurrently. In terms of airpower, the BUR concluded that production of the F/A-18 E/F and the F-22 should continue, while other programs, such as the MRF and AX/AFX, were canceled. To address the gap left by these cancellations, the Pentagon introduced a new multi-service initiative known as the Joint Advanced Strike Technologies (JAST) program. This initiative ultimately led to the development of the F-35. The Joint Advanced Strike Technologies (JAST) program aimed to consolidate multiple aircraft replacement needs into a single initiative. Its objective was to replace the USAF's F-16, F-111, and F-117, as well as the USN's F-14 and A-6. Later, after considerable debate, the USMC’s AV-8B Harrier jump jet was also included. Interestingly, one notable omission from this list was the USAF A-10. Even today, nearly 30 years later, there is ongoing debate within the Pentagon and Congress about whether the F-35 can effectively replace the A-10 in the Close Air Support (CAS) mission. Unlike previous attempts to develop a single multi-service platform, the JAST program envisioned one base design with three distinct variants. These included a conventional takeoff and landing (CTOL) version for the USAF, a carrier-capable variant (CV) for the USN, and a short takeoff/vertical landing (STOVL) version for the USMC. Additionally, some USMC squadrons would operate the USN's carrier-capable variant. The program emphasized maximum commonality across the three variants, with all models produced on a single production line. JAST and the Allies To this point, we have primarily discussed "jointness" in terms of collaboration among branches of the U.S. military. However, the JAST program extended the concept to include early involvement by key international partners. Allied nations such as Great Britain, Canada, Australia, and the Netherlands were engaged from the outset. These partners contributed funding and specific requirements for the System Design and Development (SDD) phase and were also promised "work share" opportunities during the production phases. Work share arrangements have historically been challenging, requiring extensive negotiations. These often involved a form of barter, known as "offsets." For example, a country purchasing $1 billion worth of F-35s might receive a commitment to buy $200 million of its anti-tank weapons in return. However, the JAST program adopted a different approach, emphasizing "Best Value." This system allowed contractors from participating nations to competitively bid for production work. Importantly, these opportunities extended to the entire program, not just the units purchased by the bidding country—essentially offering access to a small piece of a very large production pie. This global teaming strategy is a cornerstone of the F-35 program and represents a significant evolution in international defense collaboration. Its impact and implications will be explored further in a future article in this series. So by 1994 the JAST program was in full swing. It would be a tri service, multi national aircraft, with services and some allied partner nations contributing to development and participating in production. What could go wrong ?? The Department of Defense Development System NOTE: The System Development and Demonstration (SDD) phase we have been discussing is a older term used in the 1990s when JAST was launched, today it corresponds to what is now referred to as the Engineering and Manufacturing Development (EMD) phase in the current Defense Acquisition System. Going forward we will use EMD to describe this phase. Before continuing on to actual development of JAST and the F-35, we need to have a little discussion about how the US military designs and builds aircraft. The Department of Defense (DoD) uses a structured approach for system acquisition and development, organized into distinct phases that align with key decision points and milestones. This process, known as the Defense Acquisition System, ensures that new capabilities meet operational needs while balancing cost, schedule, and performance. Below is a detailed overview of the main phases: 1. Materiel Solution Analysis (MSA) Phase Objective: Identify and evaluate potential solutions to a validated capability need. Key Activities: Conduct an Analysis of Alternatives (AoA) to assess different approaches. Develop a Concept of Operations (CONOPS) outlining how the system will be used. Begin preliminary cost estimation and risk assessment. Define key performance parameters (KPPs). Prepare for the Milestone A decision. Exit Criteria: Approval of a preferred solution. Completion of the AoA. Entry into the Technology Maturation and Risk Reduction (TMRR) phase, contingent on Milestone A approval. 2. Technology Maturation and Risk Reduction (TMRR) Phase Objective: Reduce technology, engineering, and integration risks to a manageable level. Key Activities: Conduct prototyping and testing of critical technologies. Refine system requirements to balance capability needs with affordability. Develop initial acquisition and sustainment strategies. Begin competitive contracting for development activities. Engage stakeholders to align on system requirements and risks. Exit Criteria: Validation that critical technologies are mature (Technology Readiness Level 6 or higher). Completion of system architecture and preliminary designs. Successful Milestone B decision to proceed to the Engineering and Manufacturing Development phase. 3. Engineering and Manufacturing Development (EMD) Phase Objective: Develop, build, and test a full system prototype to ensure it meets all requirements. Key Activities: Finalize system design through the Critical Design Review (CDR). Manufacture and integrate prototypes. Conduct developmental testing to validate system performance. Refine the production process and supply chain strategies. Update the acquisition and sustainment strategies as necessary. Exit Criteria: Successful completion of developmental testing. A stable and producible system design. Approval at Milestone C to transition to production and deployment. 4. Production and Deployment (P&D) Phase Objective: Manufacture, test, and field the system to achieve Initial Operational Capability (IOC). Key Activities: Begin low-rate initial production (LRIP) to validate the production process. Conduct operational testing to ensure the system meets performance and reliability requirements in realistic environments. Ramp up to full-rate production (FRP) once LRIP goals are met. Deliver systems to the end users for operational use. Develop training materials and logistics support. Exit Criteria: Approval for full-rate production. Achievement of IOC, where the system is operationally effective and suitable. 5. Operations and Support (O&S) Phase Objective: Sustain and operate the system throughout its life cycle while optimizing performance and cost. Key Activities: Implement and refine the sustainment strategy, including maintenance, spare parts, and upgrades. Monitor operational performance and address issues that arise. Execute planned updates or modifications to maintain system relevance. Manage the system's eventual disposal at the end of its life cycle. Exit Criteria: System is retired or replaced. Effective disposal in accordance with environmental and regulatory standards. Key Milestones and Decision Points: Milestone A: Approves entry into the TMRR phase. Milestone B: Authorizes entry into the EMD phase and formal program initiation. Milestone C: Approves entry into the P&D phase, including LRIP. This phased approach should provide a systematic framework to ensure accountability and successful delivery of defense capabilities that meet operational needs efficiently and effectively. The key take away here is that there is a rigid, step wise, validated development system with very specific milestones to move to the next phase. Conclusion Having explored the development process of the F-35 program and the strategic and budgetary context of the early 1990s that shaped its inception, we are now prepared to delve deeper into the program's evolution. In the next installment, Origins Part II, we will examine the formalization of the Joint Advanced Strike Technology (JAST) concept and its transition into a defined set of requirements. This period marks the commencement of the Engineering and Manufacturing Development (EMD) phase, a critical stage in the program's life cycle. The EMD phase culminated in the creation of two competing prototypes, the X-35 and the X-32. These groundbreaking designs ultimately set the stage for one of the most significant and high-profile aircraft fly-offs in aviation history—a competition that would determine the future of the F-35 program and reshape modern military aviation. Stay tuned ! References Barret & Carpenter. Survivability in the Digital Age : The Imperative for Stealth, The Mitchell Institute for Aerospace Studies, Air Force Association, July 2017 Burbage,Clark, & Pitman. F-35 The inside story of the Lightning II. SkyHorse Publishing, 2023.
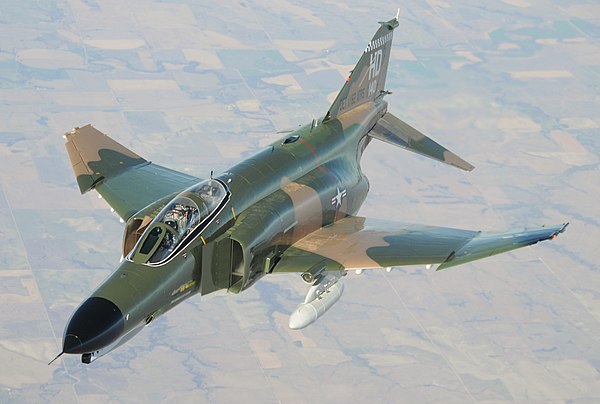